I designed and engineered many elements of Ascend, a robotic knee brace for people suffering from knee pain.
Inventing a connector from the ground up
Roam’s knee braces are driven by pneumatics—the system inflates and deflates a balloon (a very special and proprietary balloon) behind the knee of the user, applying torque to support and enhance the user’s activities.
Until recently, all of Roam’s products used two separate off-the-shelf connectors to connect to each brace: one for the electrical signals, and another for pneumatic connections to the brace. People renting Elevate on the ski slopes had to plug in 4 separate connectors to get started!
The dream was to combine them into one connector, but everything off-the-shelf was bulky, clunky, and not quite right.
So I designed one from scratch.
Many cycles of ideating, prototyping, and iterating led me to a final architecture:
Magnetic retention and breakaway, for ease of plugging, and for user safety
Cam-assisted release, to provide mechanical advantage for our users
Spring-loaded electrical contacts, for reliable signal transfer
A pneumatic contact with an auto-shutoff valve, to avoid scaring our users with a loud blast of air when unplugging the connector.
I worked with multiple molding, overmolding, and assembly vendors to develop the production process. I designed reliability verification tests, and performed root-cause analysis on anything that went wrong.
The production connector will be on the Ascend system when it launches.
Process photos:
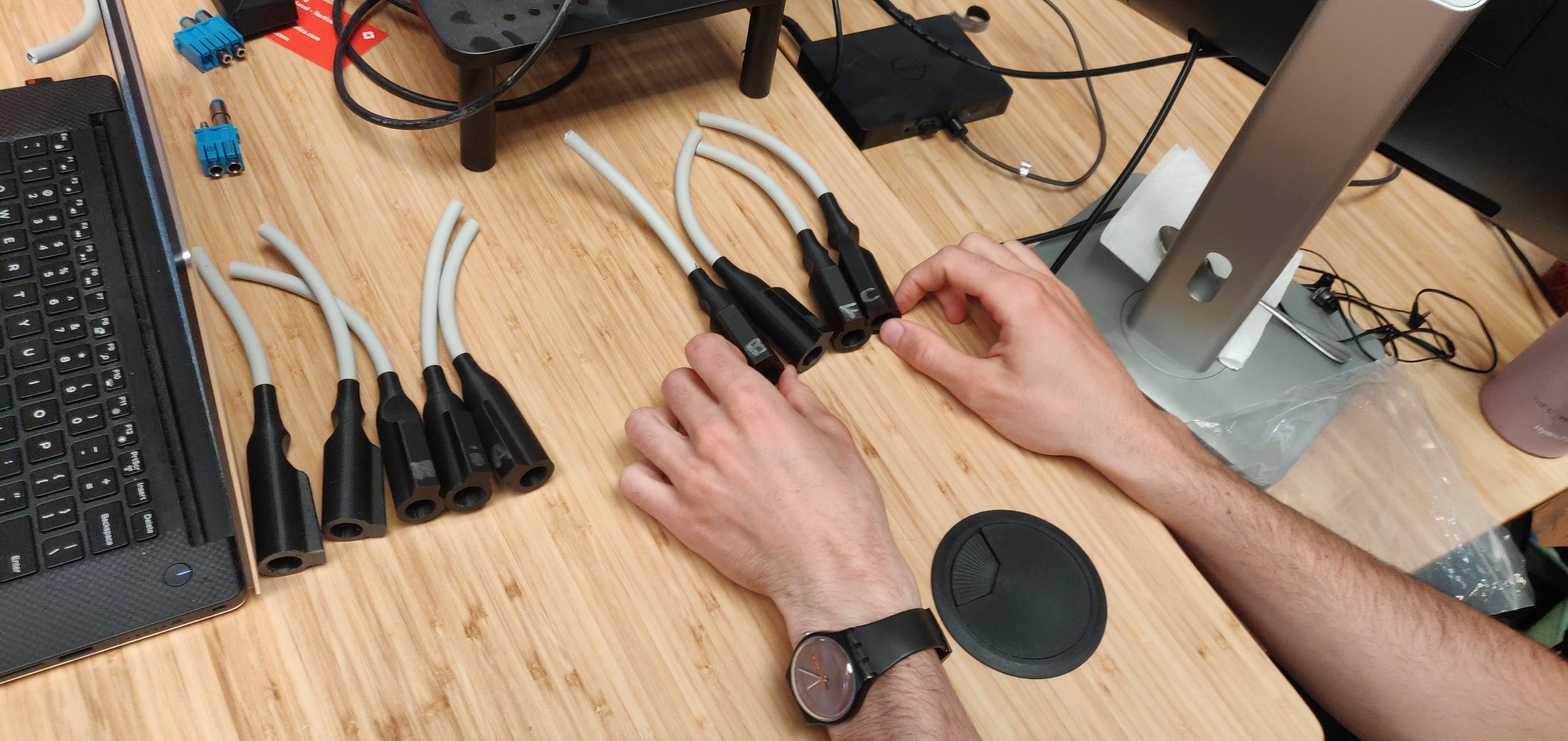
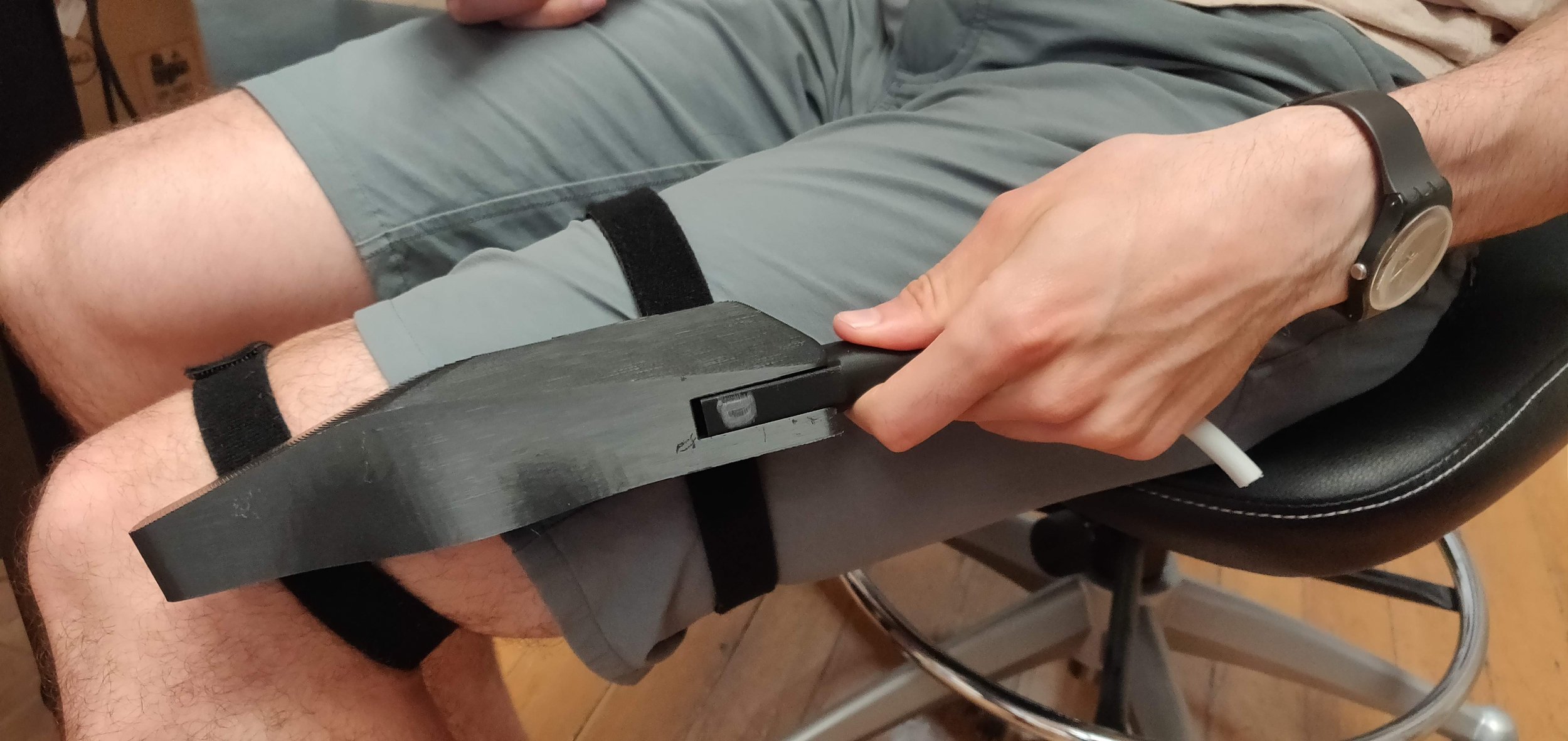
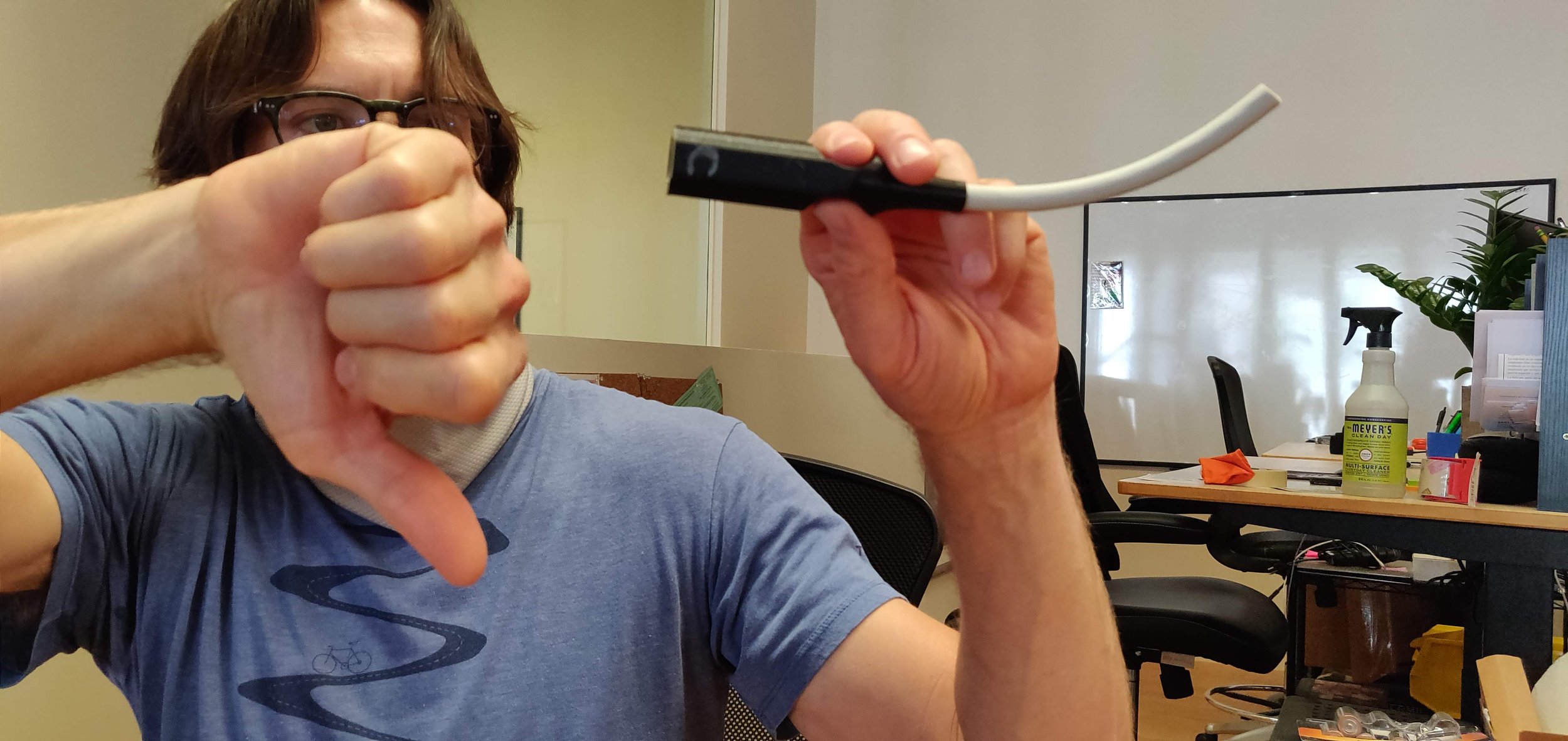
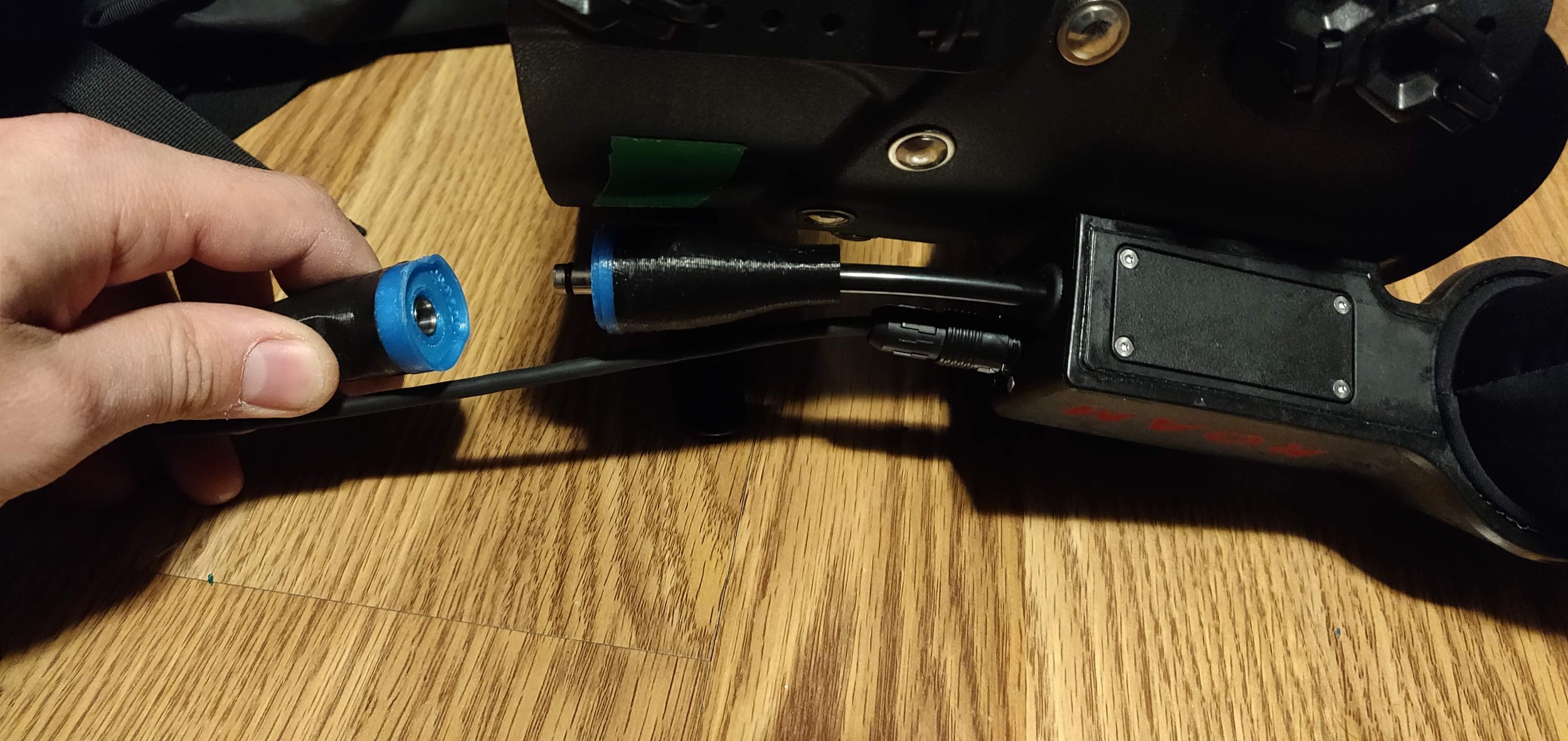
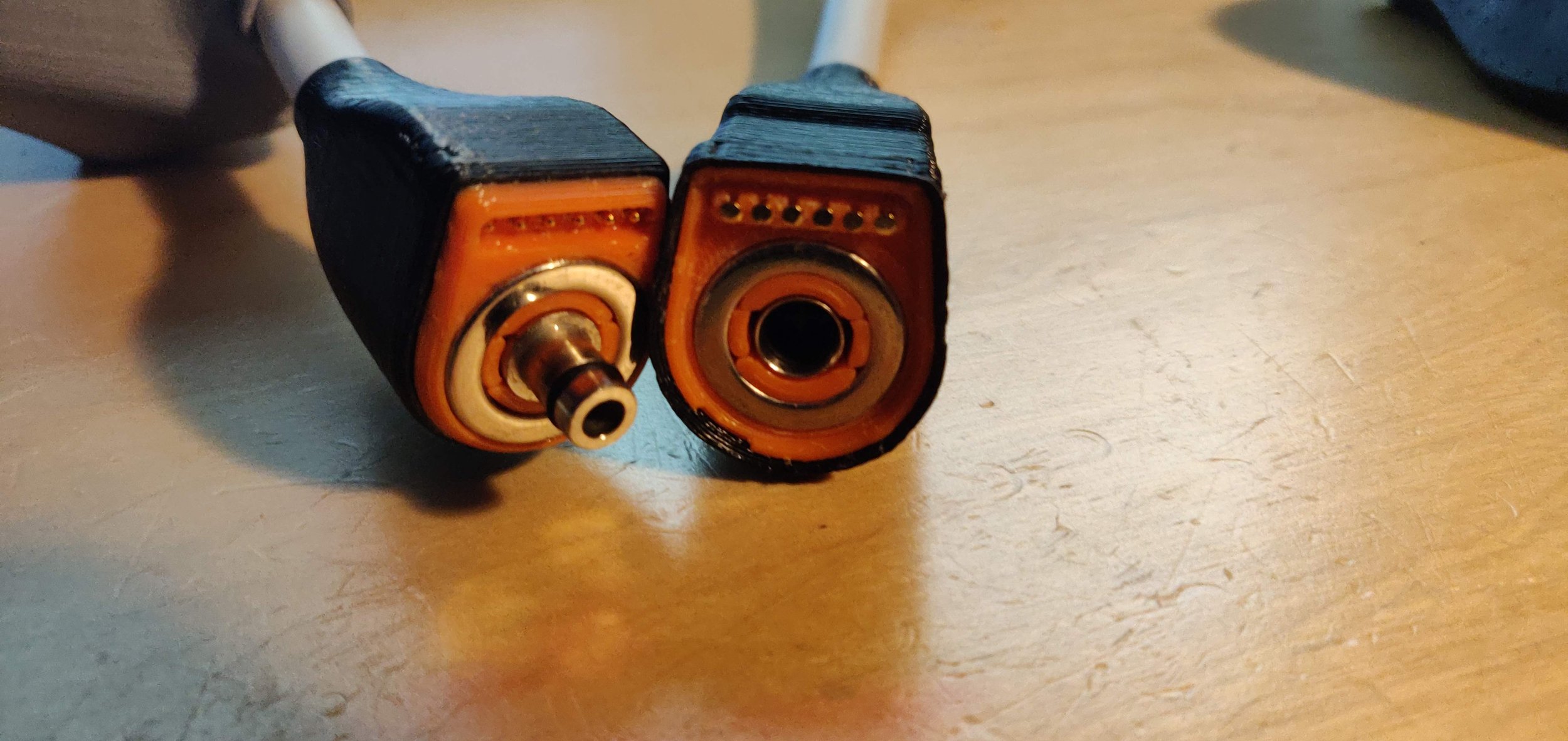
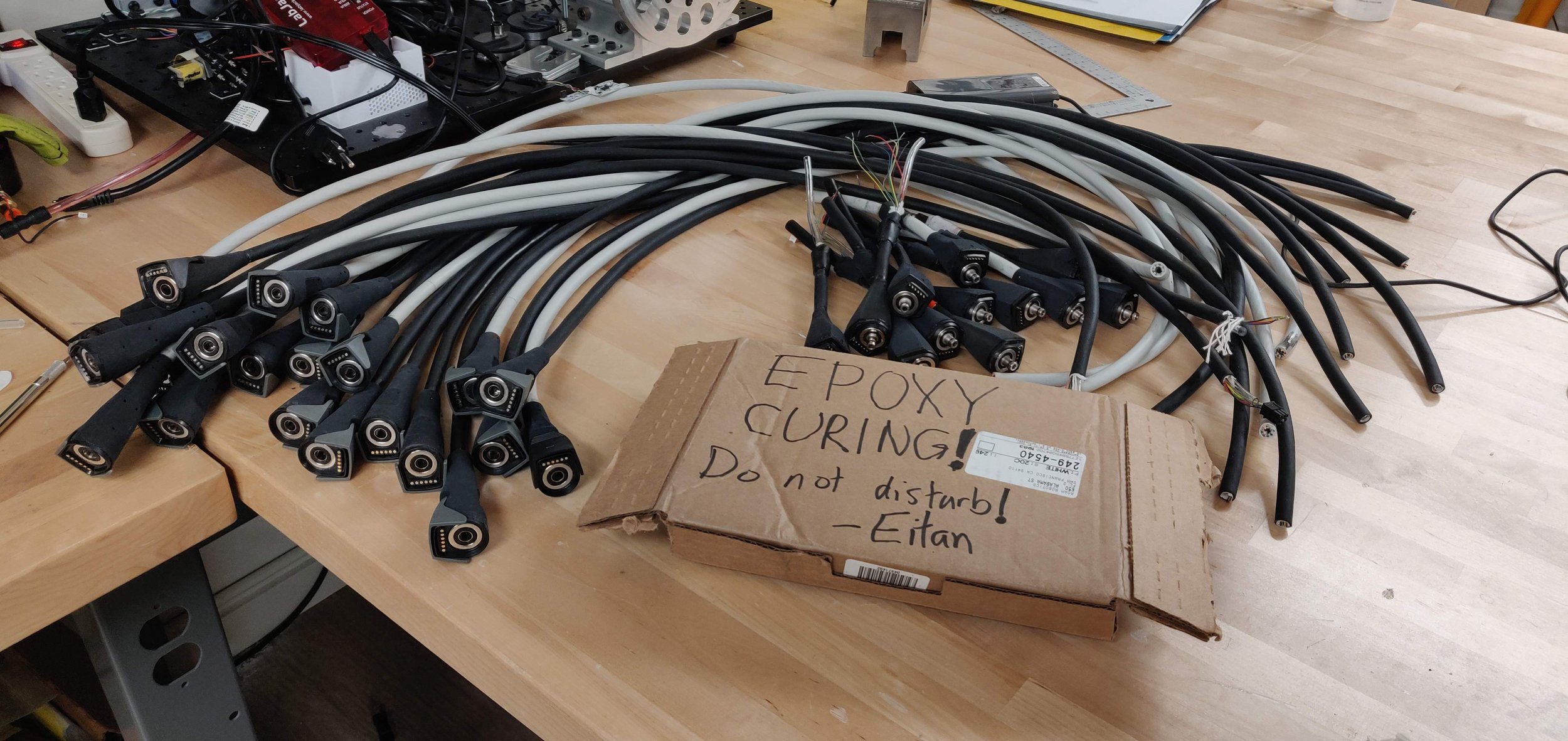
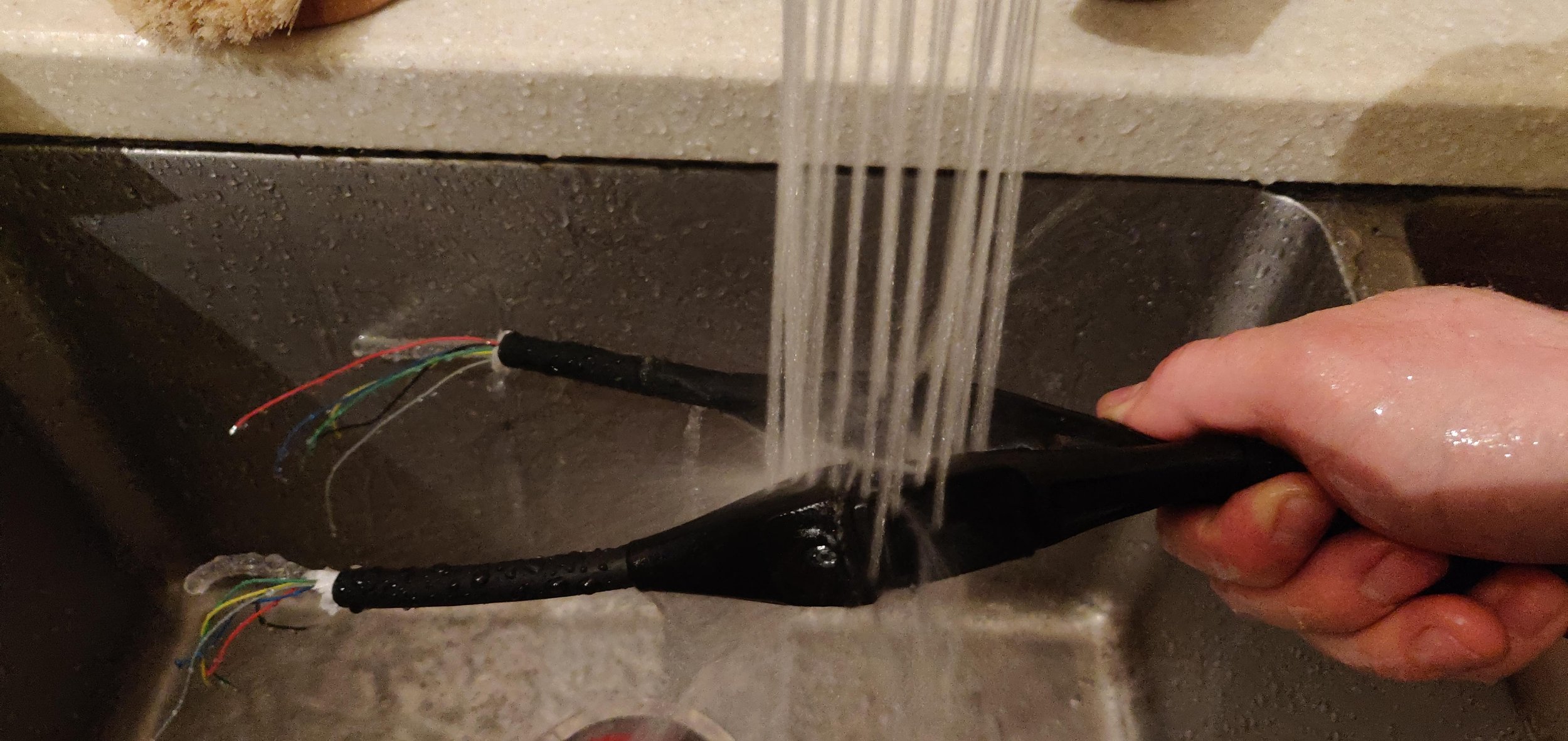
Designing a new remote
I developed a new remote design that met the unique needs of the users in the Ascend market:
Large buttons that are easy to distinguish from each other without looking.
A magnetic holster to keep the remote accessible, but out of the way.
Soft-touch, overmolded surfaces, so weaker hands can still find and grip the controls.
Long-travel button mechanisms, to avoid accidental presses, and provide strong feedback.
Robust architecture to survive all the bumps and scrapes of everyday life.
This remote involved many multi-shot components, including a three-shot front housing, with an insert-molded acrylic window, and a TPE overmold for sealing and protecting the buttons. I worked closely with our molding vendor, tuning the design and molding parameters over multiple rounds of samples, until the parts came out perfectly.
Process Photos:
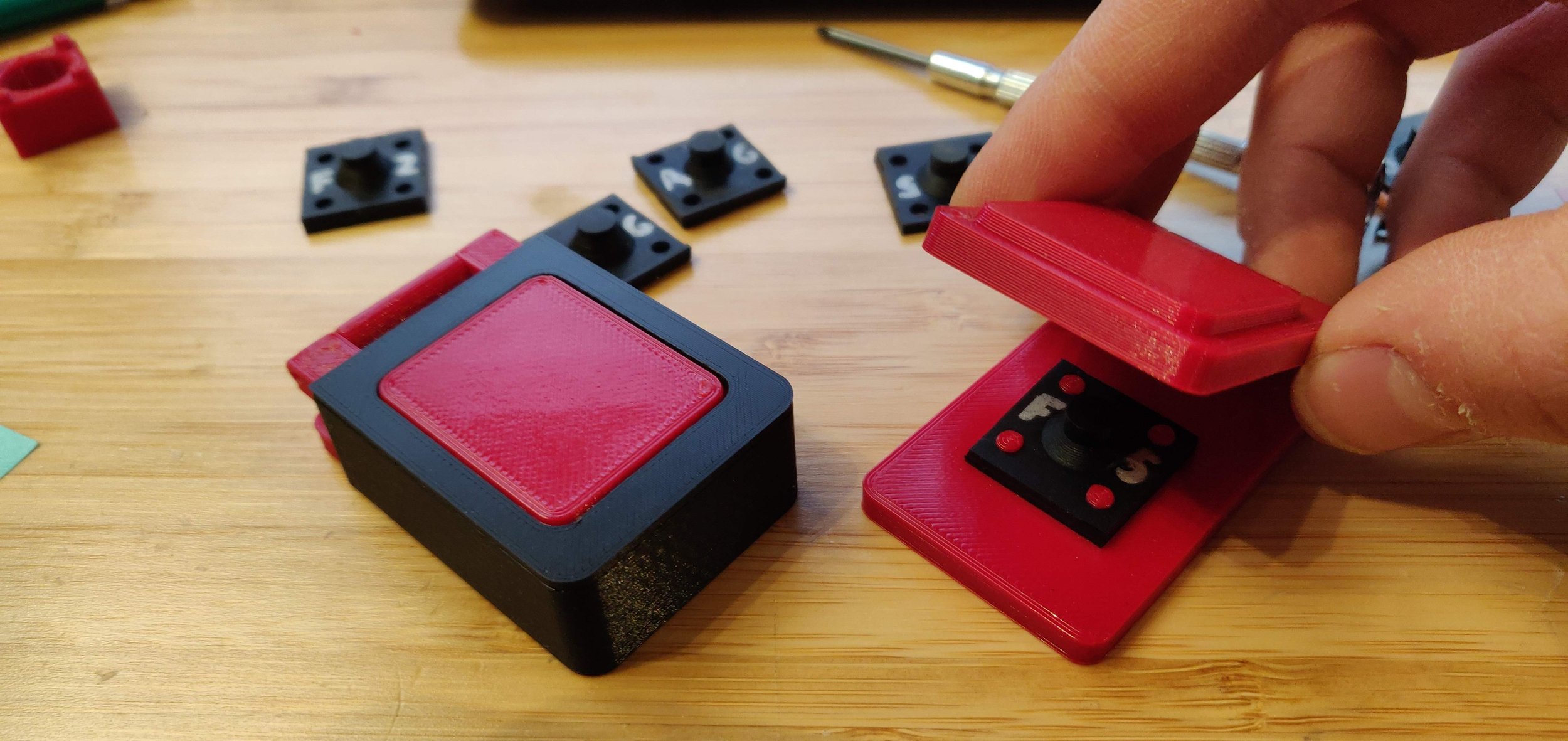
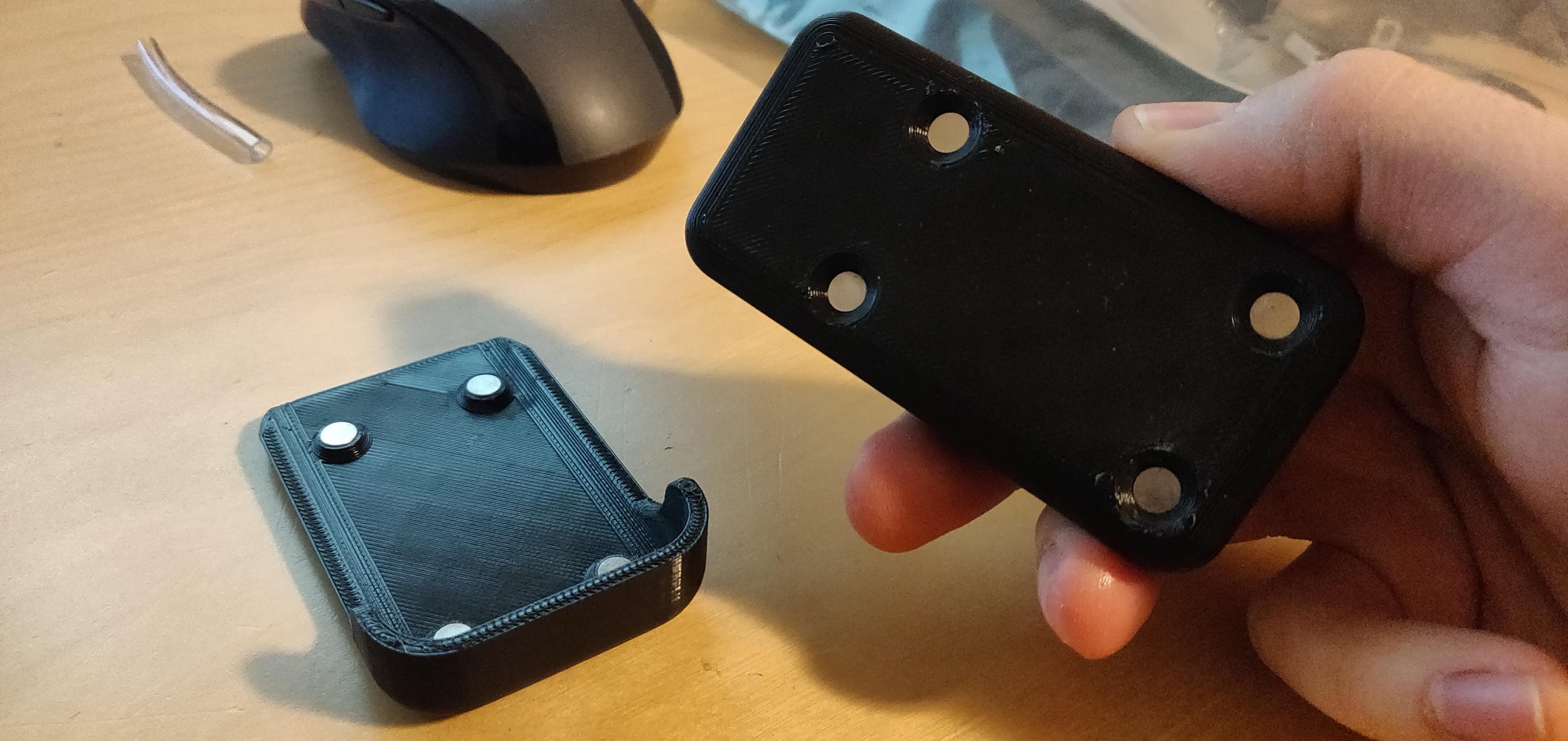
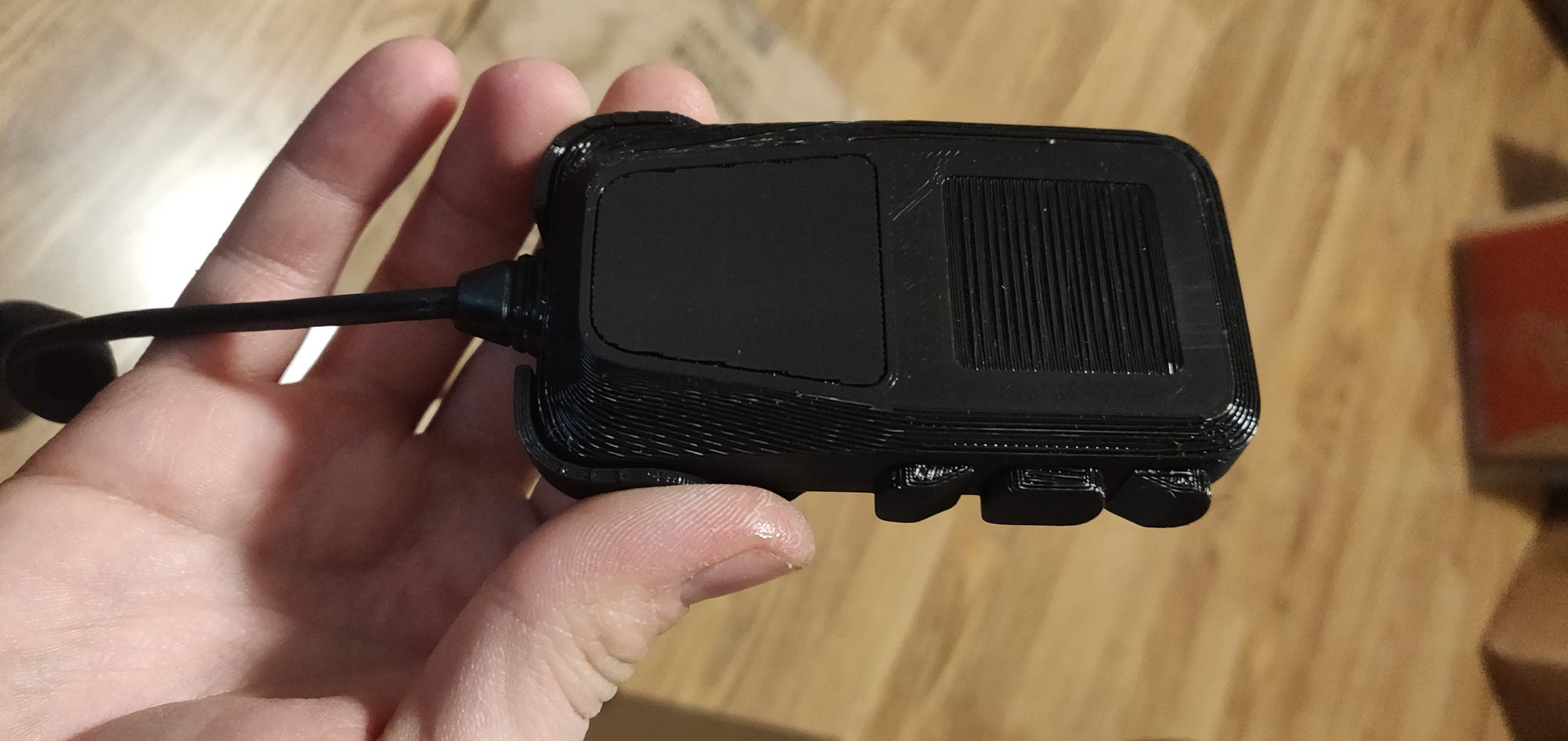
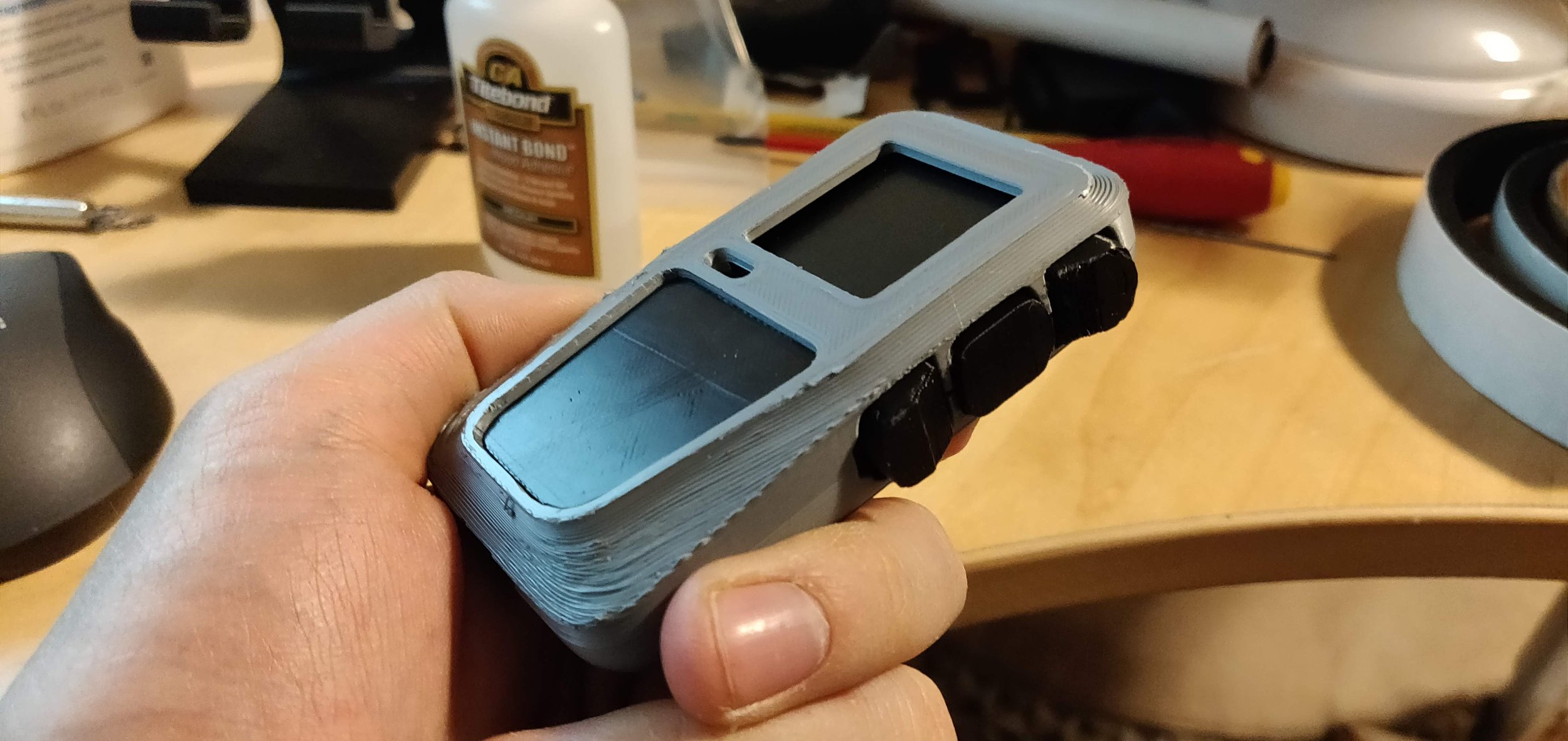
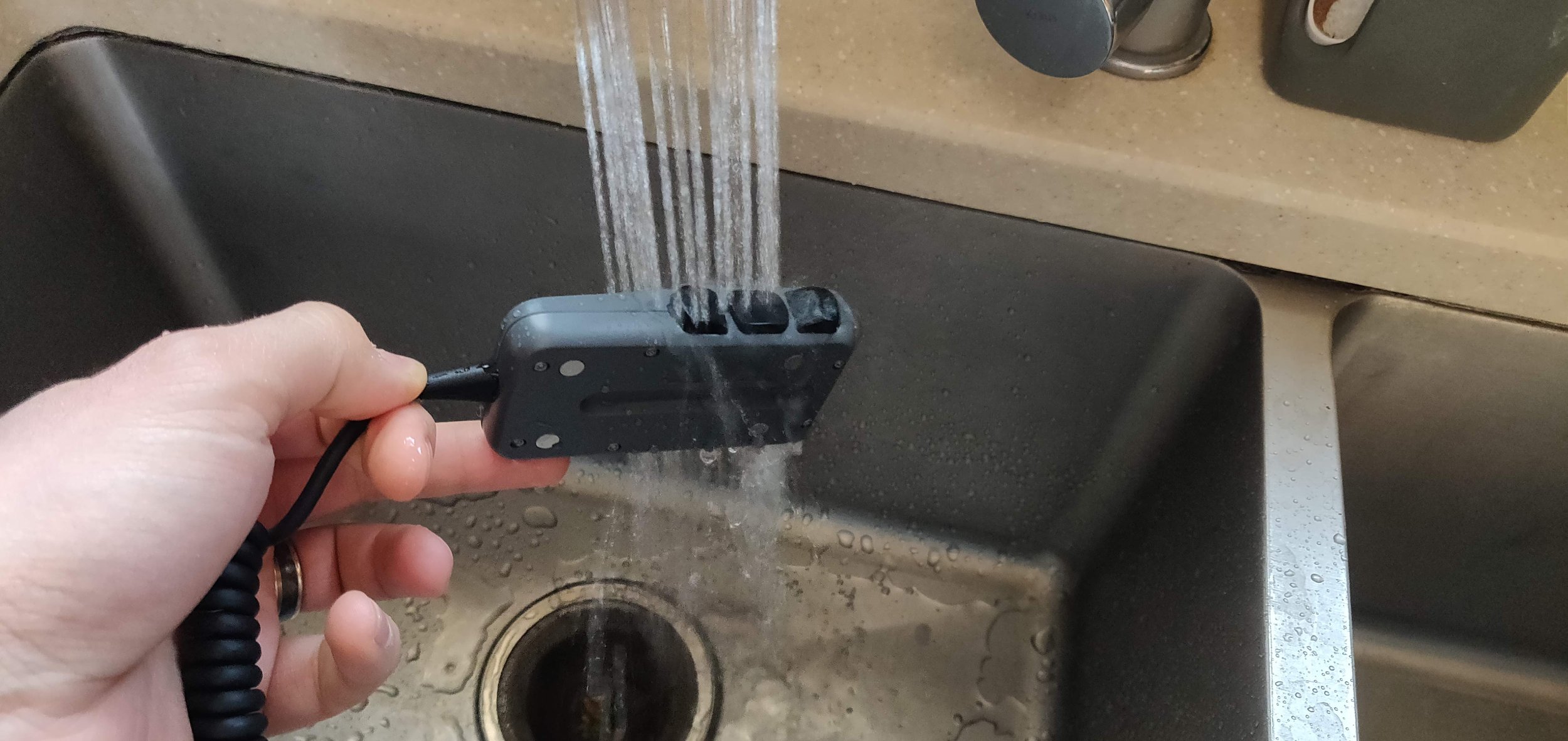

Documentation
I wrote and compiled pages and pages of documentation for the Ascend system, including assembly instructions for our manufacturing team, inspection and testing instructions for our quality department, and the official Instructions for Use (owner’s manual) for the end-user. When writing documents such as these, I carefully adapt my tone to fit the intended reader: I know how to be precise and detailed for our assemblers and testers, and how to cut out the jargon and unnecessary information so as not to overwhelm our users.
working remotely
One last note about my work on Ascend. Roam Robotics is located in San Francisco, CA. However, all of the work shown on this page was performed while working remotely full-time from my home office in Minneapolis, MN. The COVID-19 pandemic has taken a tragic toll in lives and livelihoods, but one strange silver lining is that many companies have discovered that Mechanical Engineers can successfully work remotely.
Images and video copyright Roam Robotics 2019-2022.